Organic Rankine Cycles (ORC)
Energy from waste and other heat sources. In the drive to improve energy efficiency and reduce CO2 emissions, utilisation of energy from waste heat sources, geothermal, and hydrothermal reservoirs are increasingly being exploited using Organic Rankine Cycle systems.
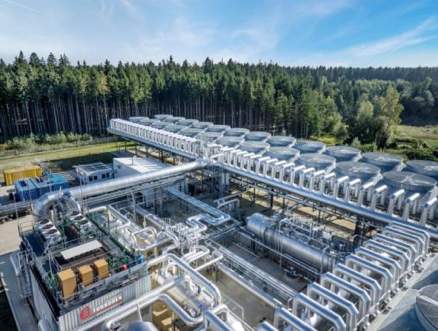
The higher boiling point fluorocarbon fluids are particularly suitable as working fluids in ORC systems as they have a good balance of safety and technical properties. These include HFC-245fa, HFC -365mfc, HCFO-1233zd(E), HFO-1336mzz(E) and HFO-1336mzz(Z). The safety characteristics of fluorocarbon working fluids offers distinct advantages and may be required for some ORC systems due to the large working fluid charge and/or the ORC location (for example for ship applications).
The difference between a high temperature heat pump and an Organic Rankine Cycle system. A heat pump upgrades lower temperature heat source and lifts it to a higher temperature, whereas the Organic Rankine Cycle (ORC) converts waste heat to power (mechanical or electrical). Waste heat sources occur in commercial and industrial operations, and mobile and stationary internal combustion engines. Low-grade temperature ORCs have widely been adopted and they come in various sizes, from several kWs to MWs. ORC systems can provide significant environmental benefit by capturing waste heat for electrical or mechanical power thus reducing fossil fuel dependency or improving overall energy efficiency.
HFC-245fa is widely being used as an ORC fluid. Both HCFO-1233zd(E) and HFO-1336mzz(Z) exhibit similar technical properties to HFC-245fa but have very low GWPs (≤2), good safety characteristics (non-flammability and low toxicity, and are therefore classified under ISO 817 and ASHRAE 34 as A1. Both have good stability at the ORC operating temperatures.
Organic Rankine Cycles can use a range of different working fluids, depending on their properties and the source temperature. These include hydrocarbons such as toluene, siloxanes and fluorocarbons. The possibility to select the fluid properties allows for the design of the components and system to optimise efficiency.
An ORC schematic is shown in the figure. The organic working fluid in the evaporator is heated by the waste heat source into a vapour state. The heated vapour enters the turbine expander which is used to generate power. After expansion, the working fluid is cooled in the condenser to the liquid state and pumped to the evaporator (or boiler).
The high temperature steam Rankine cycle is widely used in the power generation industry, using high temperature waste heat sources and at these temperatures steam is an efficient working fluid and is stable. The use of organic compounds in the Organic Rankine Cycle enables the cost-effective extraction of energy from lower temperature heat sources (typically in the range 80°C to 200°C). Compared to steam, suitable working fluids for the Organic Rankine Cycle have high molecular weights and low boiling points. These fluids enable the extraction of energy from low temperature waste heat sources using less costly simpler design systems. The conversion rate from thermal to electrical power varies depending on the choice of the best working fluid for the waste stream, the selection and optimization of the best plant layout and components, and the effects of fluid properties on expander efficiency, but typically is between 10% and 15%, including the electrical power required to drive fans and pumps in the system[1].
[1] UNEP 2014 Report of the Refrigeration, Air Conditioning and Heat Pumps Technical Options Committee 2014 Assessment Report page 105